
Testing Deliverables
Below, is attached the testing deliverables desired and actual results conducted in the spring of 2020.

Testing Methods
During the drop test, the device was at a specific controlled height using a tape measure and then the wall was marked with tape to have consistency when testing. The device had calculations to collect impact velocity and energy for each trial. The device was weighed to meet the 7 lb. weight predictions and to allow for the use of kinematic equations. The actual weight was approximately 6.51 lbs. Per instructed manufacturers procedure, the shocks on the device were filled with the proper fluid and purged to get the air out of the shocks to allow for the shocks to were properly and as intended. The shocks being filled dampened the force and energy sustained upon impact during the drop test and to accurately reflect the test of being able to withstand 14.22 J of energy. The device was then dropped and recorded to gather data and velocity. Ensuring the height of the device being dropped from was important to maintain accurate results. When calculating the deflection distance, the max travel of the springs compressed was used. A visual inspection of the components on the car were also conducted for any failures that restrict the operation of the vehicle. Rolling the device ensured that the device was properly working and the examination of joints, mating materials, and connections were inspected closely. Then, the device was tested during operation to make sure all pieces, connections, and joints are working properly. This test was conducted three times to ensure structural strength is not compromised and to simulate the Baja car jumping off obstacles during the ASME competition. During the front impact test, the device moved at a velocity of 15.6 mph, lower than our required velocity, and hit an obstacle head on to simulate obstacles within the ASME competition. Ensuring that there is enough space for testing is important to limit the dangers of possible debris and proper precautions of protecting the walls or property if testing is conducted within the Hogue Technology building. Obtaining a load cell and attaching the cell to the front of the car would be most ideal but was limited in availability and cost, so it was not included during testing. Also gathering a device such as a radar gun to ensure appropriate velocity is maintained would satisfy testing methods but also was not included due to supply chain lead times and cost. A visual inspection also took place after the vehicle sustained a front collision. The front impact test was conducted three times to confirm that the vehicle could sustain impact and maintain proper operation as intended.
Operational Limitations and Testing Issues
The RC car was not able to meet the 20 mph velocity initially, due to the car's wiring from the receiver and ESC. After a certain velocity and time frame, the car was shutting off or the power seemed limited. Testing was conducted due to time constraints with successful deliverables but the output of the device and potential was deemed unsatisfied. Rewiring the battery, ESC, and receiver allowed for a lot more throttle and speed to be reached. The RC car no longer shut off and reached speeds of 20 mph+. Unfortunately, the data reported is still accurate and consistent to the car during the testing time frame, but much more potential could have been reported to SOURCE and all supplemental reports.
Precision and Tolerances
All dimensions and tolerances in accordance to the parts manufactured or assembled are associated to the parent drawing. Based off the use of kinematic equations, the use of a stopwatch was needed to find time. Manually starting and stopping a stopwatch caused inaccuracies within the testing environment. A tolerance of ±0.50 seconds was used due to the range experienced upon starting and stopping the timer. When measured distances were involved, the tolerance of ±0.25 inches were used due to a tape measure being used along with thick tape. The tape measure is not super precise along with thick tape being used because the precision of the measurement could have been in the exact center of the tape or on either end.
Results
Vertical Drop Test
The RC Baja car was able withstand a drop of 1.5 ft with no mechanical failures or breaks. The RC car was lighter than the required 7 lbs. and came out to about 6.5 lbs. The RC car was calculated to have sustained a force of about 116 lbs. upon impact with no failures. A rolling test was conducted to ensure the functionality of the car along with an overall visual inspection.
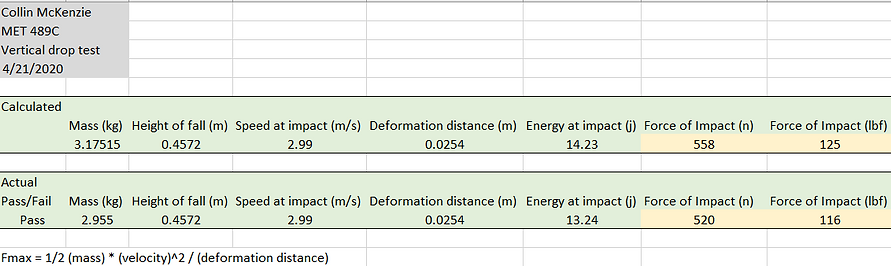

Front Impact Test
The front impact test was more efficient as trials were conducted. The car did not quite meet the required 20 mph speed but maintained functionality after collisions which was the main priority of the test, to see the longevity of the device after collision. Calculations based off tested results provided that the RC car had an average velocity of 15.6 mph and had an impact for of 842 lbf. The sustained impact of the RC car was surprising, due to most of the impact area being the rubber wheels which absorbed most of the energy and impact force.

